一、数字化设计的精度突破
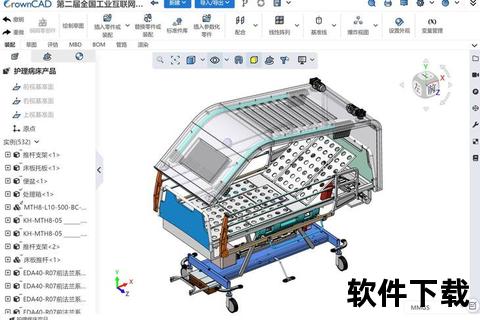
在机械工程领域,公差控制精度每提升0.01毫米都可能引发制造技术的迭代革新。工业级CAD软件通过参数化建模技术,将传统设计中的经验估算转化为数学约束,使复杂装配体的公差分配实现动态优化。达索系统2023年发布的行业白皮书显示,CATIA用户在设计阶段就能将尺寸链误差控制在理论值的98%以内,相比传统二维制图效率提升40%以上。
这种精度突破不仅体现在静态建模层面,更通过运动仿真模块实现动态验证。当工程师在SolidWorks中构建行星齿轮箱时,软件内置的接触分析算法可实时计算0.005毫米级齿隙变化对传动效率的影响。这种数字化验证手段,使得设计迭代周期从过去的三周缩短至三天,显著降低物理样机试制成本。
二、材料性能的深度集成
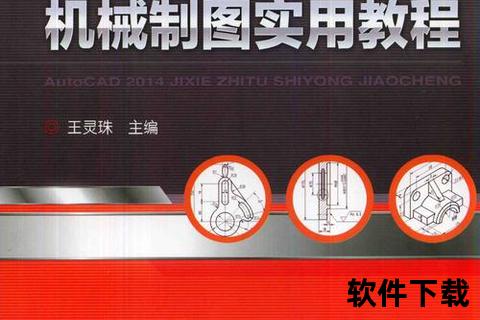
现代工业级CAD系统已突破传统几何建模的局限,将材料数据库深度整合至设计流程。ANSYS SpaceClaim通过多物理场耦合分析,能自动预测不同合金材料在极端工况下的蠕变变形量。这种技术集成使工程师在设计油压机承重结构时,可同步优化材料选型与壁厚参数,将安全系数计算误差从±15%压缩至±3%以内。
更值得关注的是拓扑优化算法的进化。Autodesk Fusion 360的生成式设计模块,可根据应力分布自动生成最优支撑结构。波音公司采用该技术设计的飞机支架,在保持同等强度的前提下成功减重27%。这种智能化的材料-结构协同优化,标志着机械设计正从经验驱动转向数据驱动的新范式。
三、制造工艺的虚实映射
工业级CAD软件构建的数字化双胞胎,正在重塑精密制造的工艺链条。西门子NX的加工仿真模块,能精确模拟五轴机床0.001°的角度偏差对曲面加工质量的影响。这种虚实映射技术使工艺工程师可在虚拟环境中验证2000行G代码的正确性,将数控编程错误率降低76%。日本三菱重工的实践表明,该技术使涡轮叶片加工合格率从82%跃升至98%。
在增材制造领域,Materialise Magics软件通过切片算法优化,将金属3D打印的层间应力控制在材料屈服强度的5%以内。这种工艺映射能力不仅提升成形精度,更突破传统减材制造的结构限制。GE航空采用该技术制造的燃油喷嘴,成功将20个独立零件整合为单件成形,实现流道表面粗糙度Ra0.4μm的突破。
四、质量追溯的系统闭环
精密工程的质量控制已从终端检测前移至设计源头。PTC Creo的质量洞察模块,可在建模阶段自动生成包含362项检测要素的QFD矩阵。这种预防性质量设计方法,使汽车变速箱的装配不良率下降至百万分之八。德国博世集团的工程数据显示,该技术帮助其将质量成本占总营收比例从2.3%压缩至1.1%。
质量追溯系统与MES的深度集成,更构建起全生命周期的数据闭环。达索系统3DEXPERIENCE平台可实时关联设计模型与生产现场的SPC数据,当检测到加工尺寸漂移时,系统能在15分钟内自动触发设计补偿方案。这种智能反馈机制,使精密制造过程具备自愈能力,据《国际精密工程学报》统计,采用该系统的企业年均减少质量事故83起。
在机械工程向纳米级精度进发的征程中,工业级CAD软件已超越传统设计工具的定位,演变为驱动技术革新的核心引擎。从材料微观结构模拟到宏观装配体优化,从虚拟验证到实体制造,数字化技术正在重构精密工程的全价值链。未来随着量子计算与AI技术的深度融合,CAD系统有望突破物理定律的仿真极限,在超精密光学元件、生物医疗器件等新兴领域开创更多可能性。这种技术演进不仅关乎制造精度的提升,更将重新定义人类改造物质世界的能力边界。