当传统工业软件遭遇智能时代瓶颈,谁能破局?
全球制造业正加速向智能化转型,但一个尖锐的问题始终存在:许多企业的软件系统仍停留在“数据孤岛”阶段,设备联动效率低下,生产决策依赖人工经验。据行业报告显示,2024年中国智能制造软件渗透率仅为37%,超60%的企业因软件适配性问题延迟了智能化改造。在这样的背景下,三菱软件革新力作:强力驱动智能未来新纪元 以其技术突破和生态整合能力,正在重新定义工业软件的边界。
1. 工业大脑如何实现精准控制?
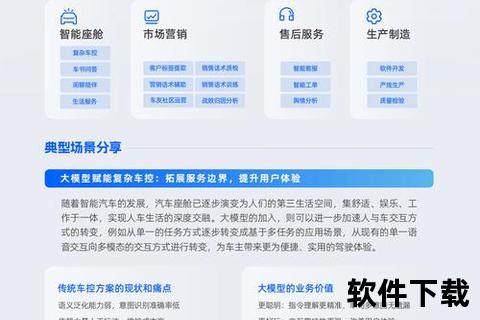
传统PLC(可编程逻辑控制器)编程依赖复杂的梯形图设计,调试周期长且容错率低。三菱推出的GX Works3软件,通过AI算法优化逻辑路径,将编程效率提升40%。例如,某汽车零部件厂商使用GX Works3控制焊接机器人,原本需要3天调试的生产线,在软件自动优化逻辑后缩短至8小时,良品率从92%提升至98%。
更关键的是,该软件支持“虚实联动”功能。用户可在虚拟环境中模拟设备运行,提前预判碰撞和流程漏洞。例如,某电子厂导入该功能后,设备故障停机时间减少65%,产能提升22%。三菱软件革新力作:强力驱动智能未来新纪元 不仅解决了精准控制难题,更将“试错成本”转化为“预判优势”。
2. 机器人编程能否更简单高效?
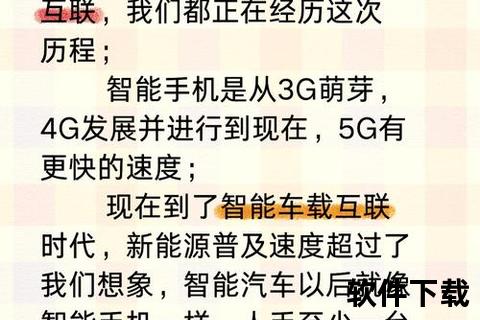
工业机器人编程长期面临专业门槛高、调试复杂的问题。三菱的RT ToolBox3 Pro软件通过“拖拽式编程”颠覆了这一现状。其内置的300+标准化动作库,允许用户像搭积木一样组合指令。某家电企业使用该软件控制装配线机器人,原本需要工程师编写的2000行代码,现在通过图形化界面配置仅需30分钟完成,人力成本降低70%。
案例显示,该软件还能通过实时数据反馈优化动作路径。某物流仓储企业部署后,分拣机器人单次抓取时间从1.2秒缩短至0.8秒,日均处理包裹量增加15万件。这种“低代码+高智能”的模式,正是三菱软件革新力作:强力驱动智能未来新纪元 的核心竞争力。
3. 数字化生态如何构建闭环?
智能制造不仅需要单点突破,更需系统级协同。三菱的MES(制造执行系统)与ERP(企业资源计划)深度整合方案,打通了从订单到交付的全链条数据。某化工企业采用该方案后,原料库存周转率提升50%,订单响应速度从72小时压缩至24小时。
更值得关注的是其“预测性维护”功能。通过分析设备振动、温度等50+参数,系统可提前7天预警故障风险。某机械制造厂应用该功能后,设备突发故障率下降80%,维护成本减少45%。三菱软件革新力作:强力驱动智能未来新纪元 以数据为纽带,正在重塑制造业的生态逻辑。
给企业的三个行动指南
分阶段实施:优先在质检、物流等痛点环节部署智能化软件,参考案例中电子厂的“虚实联动”路径,初期投入可控且见效快。
选择适配性方案:根据企业规模选择软件版本,中小厂商可侧重RT ToolBox3 Pro等轻量化工具,大型企业则需整合MES+ERP系统。
强化数据治理:建立标准化数据采集规范,避免因格式混乱导致系统兼容性问题,参考化工企业案例中的多维度参数分析框架。
全球工业4.0竞赛已进入深水区,软件能力将决定制造业的胜负手。当技术革新与场景需求深度耦合,三菱软件革新力作:强力驱动智能未来新纪元 不仅是一套工具,更是一条通向智能制造的可行路径。
--