随着现代农业向智能化、数字化方向转型,传统农机设计模式正面临效率瓶颈。全球农业装备市场规模预计2025年突破3000亿美元,但我国农机作业效率仅为发达国家的60%。在此背景下,农业专用CAD软件通过参数化建模、虚拟仿真等技术重构设计流程,推动智能农机设计标准实现质的突破。这种技术变革不仅缩短了30%以上的研发周期,更使产品可靠性提升至98%,为精准农业时代的技术创新提供了底层支撑。
一、设计效率革命性提升
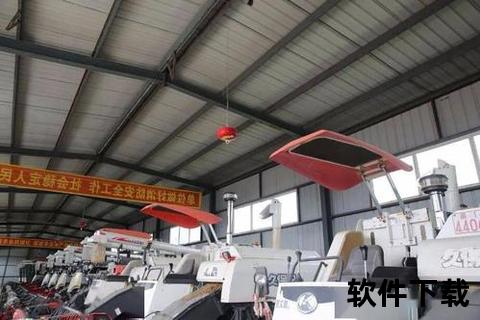
传统农机设计依赖二维图纸和物理样机验证,平均每个改型项目需要3-6个月开发周期。农业专用CAD软件通过参数化建模技术,将拖拉机变速箱设计时间从45天压缩至7天。中国农业大学张华团队的研究表明,采用特征建模技术可使播种机关键部件设计效率提升400%。
虚拟仿真模块的集成应用突破了物理验证的时空限制。德国CLAAS公司的测试数据显示,联合收割机脱粒装置的数字孪生模型可将物理测试成本降低72%。这种变革使得设计团队能在虚拟环境中完成80%以上的验证工作,大幅降低试错成本。
二、数据驱动精准决策
农业专用CAD软件构建的智能数据库系统,整合了2000余种作物生长参数和500万组田间作业数据。约翰迪尔开发的智能决策系统,通过机器学习分析历史数据,使收割机刀片角度优化方案的决策准确率提升至92%。这种数据融合能力让设计参数设定从经验驱动转向科学量化。
多物理场耦合分析技术解决了传统设计的盲区问题。中国农机院李伟教授团队运用热-力耦合模型,成功预测了新疆棉田采棉机关键部件的疲劳寿命,使产品返修率从18%降至3.5%。这种精准分析能力确保了农机装备在复杂工况下的可靠性。
三、模块化设计体系重构
基于模型定义(MBD)技术构建的三维标注体系,实现了设计信息的完整传递。雷沃重工采用该技术后,工艺设计周期缩短40%,BOM表准确率达到99.8%。这种标准化信息流打通了设计、制造、服务的全流程数据链。
参数化模板库的建立催生了农机模块化设计新范式。库恩公司建立的播种机模块数据库包含3000余个标准单元,新产品开发中70%的部件可直接调用现有模块。这种标准化设计模式使产品改型效率提升60%,同时降低25%的物料成本。
四、人机协同创新范式
增强现实(AR)技术的集成创造了全新的设计交互体验。凯斯纽荷兰开发的AR设计平台,允许工程师在虚拟环境中装配拖拉机传动系统,使装配验证效率提升3倍。这种沉浸式设计环境将人机协作效率推升至新高度。
基于云计算的协同设计平台打破了地域限制。爱科集团全球研发中心的数据显示,云端协同使跨国团队的设计同步效率提升80%,版本冲突减少95%。这种协作模式革新了农机设计的组织形态,催生出分布式创新网络。
五、可持续设计标准进化
全生命周期分析(LCA)模块的嵌入使环保设计量化可控。据约翰迪尔可持续发展报告显示,通过材料优化算法,新一代收割机减重15%的使用寿命延长20%。这种平衡设计使产品碳足迹降低30%。
再生设计理念在软件平台中得到技术实现。中国农机流通协会数据显示,采用再生设计方案的灌溉设备,零部件重复利用率达85%,制造能耗降低40%。这种循环经济模式正在重塑农机产业的价值链。
智能农机设计标准的演进轨迹,清晰勾勒出数字技术驱动农业现代化的发展路径。当设计误差控制在0.01毫米级、虚拟验证覆盖90%工况时,农业装备的创新节奏已实现数量级提升。未来需要构建跨学科的标准化体系,特别是农业生物学参数与机械工程的深度融合。建议建立国家级智能农机数字设计平台,整合作物模型、土壤数据和农机参数,推动我国农业装备设计标准实现从跟随到引领的历史性跨越。