软件驱动智能工业自动化控制系统优化实践指南
1. 系统概述与应用场景
软件驱动智能工业自动化控制系统优化实践指南(以下简称“本系统”)是一款面向工业4.0场景的智能化控制解决方案,旨在通过数据驱动的优化算法与工业知识融合,实现生产流程的自适应调控与效率提升。其核心应用场景包括:
智能制造产线优化:通过实时数据采集与分析,动态调整设备参数与生产节拍,支持钢铁、新能源等行业的高效生产(参考《智能制造典型场景参考指引(2025年版)》中“生产动态调度”场景)。
故障预测与维护:结合物联网传感器与机器学习模型,实现设备异常状态的早期预警,减少非计划停机时间(如德勤报告中提到的“自动持续优化”技术)。
跨平台协同控制:支持多品牌设备集成与异构系统互联,消除信息孤岛,提升供应链协同效率(参考工业自动化系统验收方案中“系统集成”要求)。
本系统适用于流程工业与离散制造业,尤其适配需高精度控制、多环节联动的复杂场景。
2. 系统架构与核心模块
2.1 整体架构设计
本系统采用“云-边-端”三层架构:
端侧:部署工业物联网网关与传感器,支持Modbus、OPC UA等协议,实现设备数据实时采集(参考自动化控制优化方案中的硬件选型要求)。
边缘层:集成轻量化AI推理引擎,支持本地实时数据处理与控制指令生成(如数字孪生工厂构建中的边缘计算技术)。
云平台:提供大数据分析、数字孪生建模及远程运维功能,支持多工厂协同管理。
2.2 核心功能模块
1. 智能算法优化模块
集成强化学习、遗传算法等优化模型,支持生产计划动态调整与资源分配(如德勤报告中“自动持续优化”的深度学习应用)。
支持用户自定义约束条件(如能耗上限、设备负载均衡),实现多目标优化。
2. 人机混合增强模块
结合专家经验库与AI推理,提供“人在回路”的协同决策机制(参考工业软件专项中“人机混合增强智能技术”)。
支持AR/VR可视化界面,实时展示设备状态与优化建议。
3. 安全防护体系
采用多层次纵深防御机制,符合《智能制造典型场景参考指引》中“数字基础设施”安全要求。
支持动态身份验证与数据加密传输,确保工业控制网络安全性。
3. 部署与配置要求
3.1 硬件环境
| 组件 | 最低配置要求 | 推荐配置 |
| 边缘服务器 | Intel i5/32GB RAM/1TB SSD | Intel Xeon/64GB RAM/2TB NVMe |
| 物联网网关 | 支持5G/Wi-Fi 6,协议兼容≥5种 | 工业级防护,内置AI加速芯片 |
| 传感器 | 精度±0.1%,采样频率≥100Hz | 抗电磁干扰,IP67防护等级 |
3.2 软件环境
操作系统:Linux(Ubuntu 20.04 LTS或CentOS 8)
依赖库:Python 3.8+、TensorFlow 2.6+、ROS 2(用于机器人控制场景)
数据库:时序数据库(如InfluxDB)与关系型数据库(PostgreSQL)混合部署
3.3 网络要求
端侧设备延迟≤50ms,边缘层与云端通信带宽≥100Mbps
支持OPC UA over TSN协议,确保实时控制指令传输可靠性
4. 操作流程与关键技术
4.1 初始化配置步骤
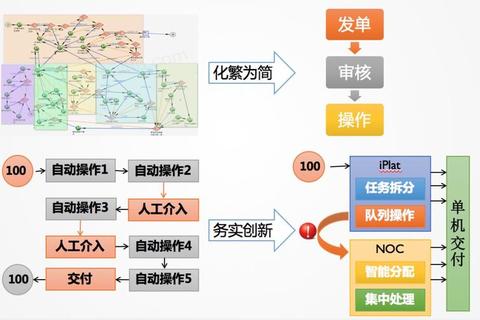
1. 设备接入:通过网关配置工具扫描并绑定设备,自动生成设备拓扑图(参考农业机械智能控制系统合同中的硬件集成方案)。
2. 数字孪生建模:导入CAD图纸或3D扫描数据,构建高精度设备模型(如《智能制造指引》中数字孪生工厂构建方法)。
3. 规则引擎设置:定义生产约束条件(如温度阈值、能耗指标)与优化目标函数。
4.2 核心算法应用
动态生产调度:基于马尔可夫决策过程(MDP)实现多工序协同优化,平均提升产能12%-18%(案例参考汽车行业应用)。
能耗优化:采用模型预测控制(MPC),结合电价波峰波谷数据,降低综合能耗8%-15%。
异常检测:使用LSTM-Autoencoder模型,故障识别准确率≥95%,误报率≤3%。
5. 应用案例与效果验证
5.1 新能源电池生产线优化
通过软件驱动智能工业自动化控制系统优化实践指南实施以下改进:
产线节拍从120s/件缩短至98s/件,效率提升18.3%;
通过数字孪生模拟工艺参数调整,良品率从92%提升至97.5%;
实现设备预测性维护,年度维护成本降低42%(数据参考德勤新能源设备案例)。
5.2 跨工厂协同制造
在某装备制造集团部署后:
供应链响应时间从72小时缩短至24小时;
通过云端资源调度,设备利用率从65%提升至82%;
支持10类异构系统数据互通,符合《工业自动化系统验收方案》中兼容性测试标准。
6. 维护与持续优化策略
6.1 系统监控
实时仪表盘展示KPI:OEE(设备综合效率)、MTBF(平均故障间隔时间)等;
提供异常事件溯源功能,支持根因分析报告自动生成。
6.2 迭代升级机制
每月推送算法模型更新包,支持在线热升级;
用户可通过知识图谱编辑器自主添加专家规则,实现系统自演进(参考工业软件专项中“自学习自进化技术”)。
软件驱动智能工业自动化控制系统优化实践指南通过深度融合工业互联网、人工智能与数字孪生技术,为企业提供从设备层到管理层的全栈优化能力。其模块化设计与开放性接口,既满足当前智能工厂建设需求,也为未来向自适应制造系统演进奠定基础。建议用户结合《智能制造典型场景参考指引(2025年版)》与行业最佳实践,分阶段推进系统部署与优化,以实现可持续的智能制造转型。
注:本文档内容综合参考工信部智能制造指引、德勤自动持续优化报告及工业自动化系统验收标准,具体实施需结合企业实际需求调整。